Le Moulage sous pression en métal Le processus peut produire des produits de forme complexe et peut offrir une excellente précision dimensionnelle et une excellente finition de surface. Il s'agit également d'un processus de fabrication très efficace et peut rivaliser avec d'autres méthodes de fabrication. La machine de moulage sous pression comporte une moitié fixe ou de couverture et une moitié d'éjection qui contient un trou d'injection, une porte et un système de canaux. Le métal en fusion est injecté dans les matrices où il refroidit et se solidifie pour devenir le produit fini. Le moulage sous pression offre un certain nombre d'avantages qui en font une option attrayante pour la fabrication. Ses coûts d'outillage sont inférieurs à ceux des autres processus de fabrication et vous permettent de produire des pièces avec des tolérances étroites. Il élimine également le besoin d’usinage supplémentaire et vous permet de créer des parois minces. Pour garantir la précision, les fabricants utilisent une série d’outils pour contrôler le processus. Ceux-ci incluent l'éjecteur, les canaux, le biscuit (ou grappe) et le flash. Ces éléments sont situés à l’intérieur de la cavité de la matrice et sont utilisés pour diriger le métal en fusion dans et hors du moule.
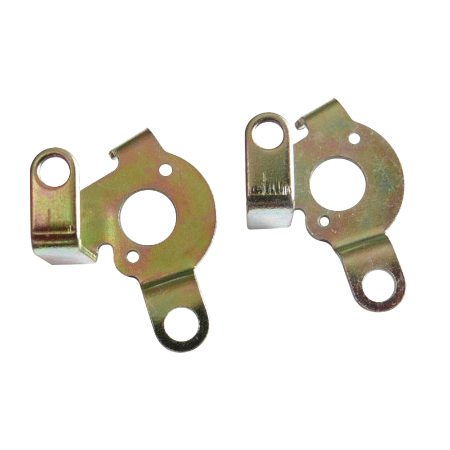
Contrairement au moulage par injection de plastique, le moulage sous pression produit des composants plus solides et plus légers. Ils sont dimensionnellement stables et peuvent supporter des tolérances serrées sans trop de difficulté. Le procédé offre également une meilleure finition que les autres méthodes de fabrication. Les fabricants soumettent souvent les produits obtenus au sablage et à d'autres traitements pour une finition impeccable. Ils sont alors prêts à être expédiés ou utilisés. Ces avantages en font un choix populaire pour de nombreuses industries différentes. Le moulage sous pression peut produire des produits de formes complexes en métaux légers avec une haute précision. Il est particulièrement utile pour les pièces qui doivent résister à des températures et des pressions élevées, telles que les composants d’équipements automobiles et médicaux. Il peut également fournir une excellente finition de surface, une porosité comparativement réduite et une précision dimensionnelle. Le processus comprend quatre étapes principales : la préparation des matrices, l'injection, le refroidissement et l'éjection. Les matrices sont pulvérisées avec un lubrifiant pour empêcher le métal en fusion d'y adhérer. Ensuite, le métal en fusion est injecté dans les filières sous haute pression. Cela garantit que le métal fondu est forcé même dans les plus petits coins du moule et atténue le retrait.
Le métal est ensuite refroidi dans le moule jusqu'à solidification. Après cela, les moitiés de la matrice sont séparées et les broches d'éjection poussent la pièce moulée hors de la matrice. Tout excédent de métal est ensuite découpé à l'aide de différents outils. La qualité de la pièce moulée sous pression dépend de sa conception et de son alliage métallique. Le moulage sous pression est un processus flexible qui peut être utilisé pour une variété d'applications. Il permet un taux de production élevé et produit une qualité uniforme qui nécessite moins de main d’œuvre que les autres méthodes de fabrication de pièces métalliques. Cette flexibilité en fait un choix populaire pour les industries automobile, aérospatiale et médicale. Les alliages métalliques utilisés dans le moulage sous pression peuvent être modifiés pour répondre à des besoins spécifiques. Par exemple, le zinc est souvent utilisé dans les pièces moulées sous pression pour garantir un point de fusion bas du métal. Il offre également une bonne résistance à la corrosion et une finition de surface lisse.
La matrice métallique est divisée en deux sections : la moitié fixe ou couvercle et la moitié éjecteur. La moitié de l'éjecteur est équipée d'un trou d'injection, d'un canal et d'une porte pour acheminer le métal en fusion dans la cavité du moule. Une tige d'étirage ou des broches d'éjection sont ensuite utilisées pour pousser le moulage sous pression hors du moule. Il est important d’éviter les contre-dépouilles dans la conception de votre pièce. Ils peuvent provoquer un retrait du métal liquide lors de la solidification, ce qui peut affecter les dimensions et la pression d'injection de la pièce. Le moulage sous pression peut être un moyen rentable de produire une pièce. En effet, une pièce peut remplacer plusieurs composants, éliminant ainsi les opérations secondaires de fraisage, d'alésage, d'alésage et de meulage. De plus, le processus est incroyablement précis et entraîne des taux de rebut très faibles. Cependant, l’investissement initial dans les moules métalliques peut être élevé. Le coût global du moulage sous pression peut être réduit en choisissant un moule plus petit avec plusieurs cavités.
Pendant le processus de coulée, le métal en fusion est injecté dans les matrices à haute pression. Cette pression est maintenue jusqu'à ce que le métal en fusion se solidifie dans la cavité de la filière. Le temps que cela prend dépend de la complexité géométrique de la matrice et de l'épaisseur de paroi souhaitée pour le produit fini. Les pièces moulées découpées sont ensuite éjectées des matrices par un système d'éjection. Le système d'éjection se compose de deux parties : les broches d'éjection et la plaque d'éjection. Il est important de choisir le bon système d'éjection pour votre projet car cela affectera la qualité finale des pièces moulées. Si les broches d'éjection sont trop faibles, elles ne parviendront pas à pousser les pièces moulées hors des matrices, ce qui entraînera une pièce coulée défectueuse.